Full automatic packaging line of parenteralia in pharmaceutical industry.
Contributed by | Stäubli Corporation
Bayer Schering Pharma chooses Stäubli robots for its automatic drug packaging line developped by Klaus Radke Industrietechnik.
The fully enclosed six axis robots allow interruption free production featuring high precision and reliability. One bag packaging line equipped with the new heavy-payload 6 axis robot TX200 benefits from the unique features of its 100 kg payload.
Bayer Schering Pharma belongs to one of the biggest pharmaceutical companies with a high international reputation. This affiliated group owns production facilities in the United States, Latin America, Asia and Europe and among these several in Germany. Based in Leverkusen, Germany, the company produces parenteralia under stringent hygienic requirements. These drugs are not for oral intake, but are dedicated to be fed to the human body by being injected, infused or by implantation. The liquids are being filled in primary bags like flasks, vials or plastic containers. Subsequently to this primary packaging the Stäubli robots pack the drugs in boxes for the shipment.
Since August 2009, two Stäubli robots have proven their performance in a packaging line for filling and packing of bags. Bayer Schering Pharma chose the RX160 and TX200 models which work reliably hand in hand without any disruption to production. The smaller model RX160 being responsible for the bag handling, the bigger one handles the empty trays as well as the trays filled with bags.
The clever interaction between TX200 and RX160 avoids production breakdown.
In order to avoid any production breakdown when replacing a tray and to allow the RX160 to deposit new bags, the TX200 robot controller manages the complete production process beginning from the buffering of the bag feeding up to the synchronization of all handling operations. This process control allows for the continuous change of the trays without unavoidable breaks and the product can constantly be treated.
The Stäubli robots have proven to be an ideal solution for use in the packaging cell. The RX160 and TX200 models are highly suitable for the process specific requirements by their fully enclosed structure which makes them easy to clean and use in clean room environments.
The excellent rigid structure of the robots allow for high dynamic performance. According to Mr. Manfred Broustin, Leader of Automatic Control Engineering of the parenteralia production plant in Leverkusen “Stäubli products offer an outstanding fit for use in a clean room environment. We feel that due to their arm compactness as well as fully enclosed surface structure, Stäubli robots are unrivalled in the market regarding cleaning capability.” The heavy-payload six axis robot TX200 is IP65 as standard. Further features are the pre-installed user lines close to the forearm as well as the specially designed controller CS8C HP. The TX200 with a nominal payload of 100 kg is ideally suited for use in the bag packaging line. The trays to be transported have a capacity of 24 bags enclosed by a massive steel frame.
Manfred Broustin confirms: “We are fully satisfied with Stäubli robots. Our requirements could not have been better fulfilled than by Stäubli.”
About Author
Stäubli is a mechatronics solution provider with three dedicated divisions: Textile machinery, Connectors and Robotics. With a workforce of over 4000, the company generates a yearly turnover surpassing 1 billion Swiss francs. Originally founded 1892 as a small workshop in Horgen / Zurich, Stäubli today is an international group with its head office in Pfäffikon, Switzerland.
The content & opinions in this article are the author’s and do not necessarily represent the views of RoboticsTomorrow
Comments (0)
This post does not have any comments. Be the first to leave a comment below.
Featured Product
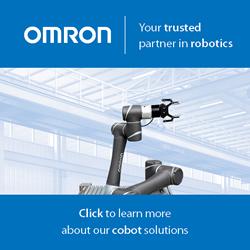