The core innovation of our new patent lies in its self-supervised approach to depth estimation. What that means is, the AI learns to judge the depth of an item it needs to pick up by using its own sensor data and the feedback it gets from its actions.
AI-Driven Grasp Depth Estimation
Q&A with Gemma Ross, VP of Operations | OSARO
Tell us about yourself and your role with OSARO
My role as VP of operations at OSARO is about ensuring our customers’ success throughout their entire journey with us. That encompasses a broad range of functions, from the initial concept development and project management, all the way through deployment, technical support, and ongoing customer success. We’re there to guide them from the very beginning and provide continuous support.
Personally, I’ve been with OSARO for six years, and my background is in computer science. It’s an interesting path, and I spent some time at DreamWorks Animation before finding my passion in robotics and AI. That experience, believe it or not, gave me a unique perspective on problem-solving and innovation, which I bring to my work at OSARO.
Can you explain the core innovation behind OSARO’s new patent for AI-driven grasp depth estimation?
The core innovation of our new patent lies in its self-supervised approach to depth estimation. What that means is, the AI learns to judge the depth of an item it needs to pick up by using its own sensor data and the feedback it gets from its actions. It’s like learning by doing – the AI doesn’t need a person to tell it if it was successful or not.
And it goes beyond just learning. Our technology also incorporates the AI’s own uncertainty about its depth estimate into how it actually performs a grasp. If you think about it, that’s incredibly sophisticated – the robot is not only learning but also factoring in its own confidence level, much like we do when we reach for something. It’s a very human-like approach to decision-making, and even some people overestimate their abilities!
How does this technology improve upon existing robotic grasping solutions in the market?
What’s truly exciting about this innovation is that it enables a sustainable robotic grasping solution for highly variable environments like fulfillment warehouses. One of the biggest challenges with AI in robotic grasping has been the reliance on specialized and often expensive sensors. On top of that, you typically need a person to constantly re-teach the AI how to grasp things whenever even a small detail changes – packaging, lighting, the shape of an item, you name it. This makes the innovation particularly well-suited to today’s dynamic e-commerce logistics and fulfillment environments.
Our patent for automated depth estimation changes that completely. OSARO doesn’t require those specialized sensors or constant human intervention. This means we can keep costs manageable for our customers while ensuring consistent, reliable performance, regardless of how much variability there is in their operations.
You mentioned that the patent allows OSARO to use less expensive cameras. How does this impact the overall cost-effectiveness and ROI for your customers? Are there any trade-offs in terms of accuracy or performance when using less specialized cameras?
It significantly changes the ROI for both our customers and for OSARO. By enabling the use of less expensive cameras, we can offer our robot-as-a-service solutions at a price point that makes automation an easy "yes" for our customers. At the same time, it allows us to meet our own cost targets, which is crucial for us as well.
Now, typically, you absolutely see trade-offs in accuracy and performance when you move to less-sophisticated cameras — and that’s where OSARO’s innovation shines. Our patented technology overcomes those limitations, enabling us to maintain high performance and accuracy without expensive vision hardware. So, in this case, we’ve essentially eliminated the typical trade-off.
What are some of the real-world challenges that this technology addresses for fulfillment and warehousing operations?
Oh, where do I start? This technology really tackles some of the most pressing issues we see in fulfillment and warehousing, especially with the explosion of the subscription economy.
Think about kitting, for example. It sounds simple, but it presents a ton of challenges. Subscription boxes are a huge trend, and that means fulfillment centers are dealing with a constant avalanche of orders with contents that change month to month, often even within the month! You might have a squeaky pet toy one month, a snack and treats box the next, and a seasonal box after that.
This creates a massive SKU management headache — and a packaging nightmare. You need to pick and pack accurately and quickly, and human workers can struggle with the constant change and the pressure to keep up. That’s where our technology comes in. Our robots can adapt to new items in real time — they can learn on the fly and handle the precise placement needed for kitting.
Another big challenge is labor. Finding and keeping people for these kinds of tasks is incredibly difficult. It’s repetitive work, and it can be tough to fill those graveyard shifts or handle unexpected surges in demand. Our robots can step in and handle those demands, providing the flexibility and reliability that human labor can’t always offer.
Ultimately, it’s about enabling our customers to meet the demands of this booming subscription economy in a way that’s efficient, cost-effective, and scalable.
Can you share any data or case studies that demonstrate the quantifiable benefits of OSARO’s technology, such as increased throughput, reduced error rates, or improved order accuracy?
Absolutely! We have numerous examples of how OSARO’s technology delivers quantifiable benefits in e-commerce applications. One compelling case is Zenni Optical. By implementing an OSARO robotic bagging system, Zenni significantly reduced order errors – we’re talking about a drop from 20 errors per 100,000 orders to an incredible 0.6 errors per 100,000 orders. That kind of precision is crucial in high-volume fulfillment of custom eyeglasses.
Beyond accuracy, our solutions also help ease the reliance on variable and temporary labor, which can be a huge challenge for warehouses, especially during peak seasons. By automating key processes, our customers can achieve greater stability in their operations and reduce the overhead associated with constantly fluctuating staffing needs.
And it’s not just about the numbers. At Zenni, the workers who used to spend their days on the onerous task of bagging eyeglasses are now in charge of monitoring the robots. They’re learning new technical skills, which is not only less tedious but also expands their career horizons. It’s a win-win: the company benefits from increased efficiency and accuracy, and the employees benefit from more engaging and fulfilling work.
What advice would you give to companies that are considering implementing AI-powered robotics automation in their operations? What are the key factors they should consider to ensure a successful deployment?
My advice would be: don’t wait! AI-powered robotics isn’t some futuristic concept: it’s here, it’s proven, and it’s delivering real results for businesses right now. While it might still seem novel to some, the technology has been deployed and tested in real-world production environments for years.
What’s particularly exciting about AI and robotics is that it’s an investment that actually gets better over time. How often do you get to say that about a technology purchase? Instead of degrading or becoming obsolete, AI-powered systems continuously improve after deployment.
Of course, choosing the right provider is critical. You need a partner who can truly unlock that AI potential and make it work for your specific needs. At OSARO, we believe our top-tier AI, combined with our robot-as-a-service model and our proactive Hypercare support, ensures that our systems consistently deliver on their promised value. Our entire company is structured around customer success, so we’re highly motivated to ensure the success of our customers.
You mentioned that the industry is changing every day. What are some of the emerging trends in AI and robotics that you find most exciting, and how is OSARO positioned to capitalize on these trends?
It’s true, the industry is evolving at an incredible pace, and at OSARO, we don’t just follow the trends – we’re actively shaping them. We see ourselves as a key driver of change in AI and robotics, particularly in how these technologies are applied to solve real-world challenges in fulfillment and logistics.
A key market driver that we’re seeing is the increasing demand for adaptable and intelligent automation. Businesses need solutions that can handle variability, learn new tasks, and optimize performance on the fly. OSARO is exceptionally well positioned to capitalize on this trend because our core focus is on providing that very kind of intelligent automation. Our AI-powered solutions are designed to be flexible, adaptable, and capable of continuous improvement, which aligns well with what the market needs.
Gemma Ross is VP of operations at OSARO, a startup in San Francisco that designs and delivers AI-driven robotics solutions for e-commerce automation. Ross oversees solution delivery and the ongoing success of OSARO’s e-commerce and 3PL customers in the warehouse, logistics, and fulfillment sectors. Her experience includes roles at Kindred and DreamWorks Animation. Ross is a graduate of Dartmouth College with a degree in computer science. Contact Gemma Ross on LinkedIn.
The content & opinions in this article are the author’s and do not necessarily represent the views of RoboticsTomorrow
Comments (0)
This post does not have any comments. Be the first to leave a comment below.
Featured Product
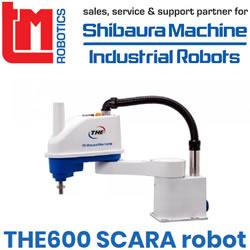