Stratasys Additive Manufacturing Solutions Selected by Airbus to Produce 3D Printed Flight Parts for Its A350 XWB Aircraft
Leading companies in a variety of industries, from aerospace and automotive to consumer goods and medical, are partnering with Stratasys to adopt additive manufacturing strategies.
MINNEAPOLIS & REHOVOT, Israel--Stratasys Ltd. (Nasdaq:SSYS), a leading global provider of 3D printing and additive manufacturing solutions, announces that leading aircraft manufacturer Airbus has produced more than 1000 flight parts on its Stratasys FDM 3D Production Systems for use in the first-of-type A350 XWB aircraft, delivered in December 2014. The 3D printed parts were used in place of traditionally manufactured parts to increase supply chain flexibility, enabling Airbus to meet its delivery commitment on-time. Airbus initiated development and certification of 3D printing with Stratasys in 2013 as a schedule risk reduction activity that proved valuable for the A350 XWB program, highlighting a key benefit of 3D printing in the manufacturing industry.
The parts are 3D printed using ULTEM 9085 resin for FDM, which is certified to an Airbus material specification. ULTEM 9085 resin provides high strength-to-weight ratio and is FST (flame, smoke, and toxicity) compliant for aircraft interior applications. This enables Airbus to manufacture strong, lighter weight parts while substantially reducing production time and manufacturing costs.
"We are delighted that Stratasys additive manufacturing solutions are being adopted by Airbus for its flagship A350 XWB aircraft. Both companies share a vision of applying innovative technologies to design and manufacturing to create game-changing benefits," said Dan Yalon, Executive Vice President, Business Development, Marketing & Vertical Solutions for Stratasys. "Our additive manufacturing solutions can produce complex parts on-demand, ensuring on time delivery while streamlining supply chains. Additive manufacturing also greatly improves the buy-to-fly ratio as significantly less material is wasted than with conventional manufacturing methods. Stratasys is looking forward to bringing these and other advantages to its collaboration with Airbus and to being part of Airbus Factory of the Future initiative."
Leading companies in a variety of industries, from aerospace and automotive to consumer goods and medical, are partnering with Stratasys to adopt additive manufacturing strategies. A transformative alternative to conventional manufacturing methods, Stratasys additive manufacturing enables original and replacement parts to be digitally produced at the best suited locations, reducing both material waste and inventory requirements. By adopting additive manufacturing throughout the product lifecycle, companies can therefore lower operational costs, accelerate time to market, decentralize production, and add new innovative product functionality.
Stratasys Ltd. (Nasdaq:SSYS), headquartered in Minneapolis, Minnesota and Rehovot, Israel, is a leading global provider of 3D printing and additive manufacturing solutions. The company's patented FDM, PolyJet, and WDM 3D Printing technologies produce prototypes and manufactured goods directly from 3D CAD files or other 3D content. Systems include 3D printers for idea development, prototyping and direct digital manufacturing. Stratasys subsidiaries include MakerBot and Solidscape, and the company operates the digital parts manufacturing service, Stratasys Direct Manufacturing. Stratasys has more than 2,800 employees, holds over 600 granted or pending additive manufacturing patents globally, and has received more than 25 awards for its technology and leadership. Online at: www.stratasys.com or http://blog.stratasys.com.
Featured Product
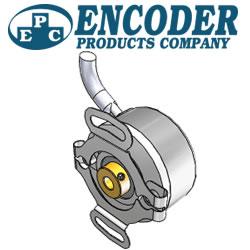