“Robotics is About People – Why You Need Change Management”
In 2020, Swiss-based Roche, one of the world's largest healthcare and pharmaceutical companies, undertook a significant robotic process automation (RPA) implementation for their Asia division. Despite substantial investment and meticulous planning, they encountered a major and unexpected obstacle: People. Roche noted that the “human side of change remains the most challenging element in managing any digital transformation. Resistance to change results in slow technology adoption, internal bottlenecks, and low return on investment.”
Even with Roche’s extensive preparation, the ultimate challenge was a culture and workforce issue. This extends far beyond the manufacturing industry, or even robotics itself – many businesses have made the same difficult choice of prioritizing technological investments over personnel. However, with this burgeoning technology rushing in to transform every aspect of business operations and reshape job roles, it's crucial to emphasize employee buy-in, cultural alignment, and a people-focused change management strategy for successful adoption.
State of Robotics in Manufacturing
Today, there are 3.4 million industrial robots in operation worldwide, and this number is rapidly accelerating. This growth signifies a transformative shift for many companies, pushing them to prepare for a future in which automation plays a central role. According to a McKinsey report, nearly 23% of jobs are at risk of automation in the next decade, with about a fifth of work activities potentially being automated. The automotive industry already utilizes extensive automation, performing tasks like welding, painting, and more through robotics, enhancing both efficiency and worker safety. As robotics becomes more accessible, other industries are likely to follow, drawn by the promise of increased productivity and asset integrity.
However, robotics still remains a developing field, and the complexity of automation presents significant challenges. Many manufacturing business owners assume the primary challenges of robotic process automation to be technical: implementation, integration, cost, troubleshooting, and training. These concerns are understandable, given the technology-heavy nature of these issues. As a result, organizations often focus mainly on these same minutia, appointing technical experts to lead these initiatives. These leaders are typically engrossed in technical details, such as granular data, metrics, and efficiency.
Conversely, employees within manufacturing units often express concerns about how automation affects their day-to-day work and job security. This disparity in perspectives—between management's focus on advancement and employees' concerns about their immediate interests—can create tension and resistance. When employees feel ambivalent or anxious, they may resist new technologies, leading to low morale and reduced productivity. This resistance can ultimately cause the failure of many automation initiatives, as the human element is foundational to successful implementation.
Bridging the Gap Between People and Process Automation
According to one labor market study from 2024, “40% of industry respondents say they still don’t have enough warehouse workers to meet demand.” In other words, robots aren’t likely to be replacing jobs en masse any time soon. Instead, there’s enormous potential for workers to get much-needed help for an already-strenuous job, making their work-life easier and more productive.
However, just because people’s fears are misplaced doesn’t mean they’re wrong. In a workplace where employees take pride in their work, develop relationships, and spend time every day, the sudden appearance of robotics can be abrasive, even scary. The fear of losing jobs to automation is a significant worry for many workers, who see robots as potential threats to their livelihoods. This anxiety, rooted in the perception that machines might render human skills obsolete, is a major barrier against adoption. If left unaddressed, this will undermine the entire transformation project.
Business leaders must recognize these concerns and take proactive steps to address them. It's essential to engage employees early in the automation process, providing clear communication about how technology can enhance their roles rather than replace them. Offering training and upskilling opportunities empowers employees to adapt to new technologies, enabling them to work alongside robots effectively.
Involving employees in decision-making and addressing their concerns transparently fosters a culture of trust and collaboration. By prioritizing a people-focused change initiative, companies can ensure the successful integration and acceptance of robotics in the workplace. This approach leads to a more harmonious and productive environment, where both technology and human talent thrive together.
Success in Robotics is All About People
Success in robotics is fundamentally about people, which is why change management is crucial for any organization considering RPA implementation. Change management experts are essential in bridging the gap between technological advancements and the workforce that will see it through.
They focus on the human side of transformation, ensuring that employees are prepared for change and actively involved in the process. They help organizations navigate cultural shifts, aligning new technologies with existing workflows and company values. This alignment is crucial for fostering an environment where employees feel valued and empowered rather than threatened by automation.
A successful change management strategy involves clear communication, early employee involvement, training and upskilling opportunities, and establishing support systems. By prioritizing these elements with a dedicated change expert, organizations can ensure a genuine and holistic company transformation, creating a harmonious and productive environment where both technology and human talent thrive together.
Joy Taylor is the Managing Director of Consulting at alliant. Specializing in succession planning, change management, and program transformations, she’s consulted for enterprises including Merck, Johnson & Johnson, W.L. Gore, Fidelity Investments and more.
Dhaval Jadav is the co-founder and CEO of alliant. Under Jadav’s leadership, the firm has empowered 24,000+ companies in 70+ industries with actionable business solutions. Prior to founding alliant, Jadav developed his expertise in high-tech business deals as a member of a Mergers & Acquisitions/Private Equity/Strategic Buyer Services Group in San Francisco and honed his business operations acumen with Deloitte & Touche in its Washington National Office.
Comments (0)
This post does not have any comments. Be the first to leave a comment below.
Featured Product
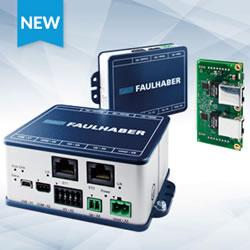